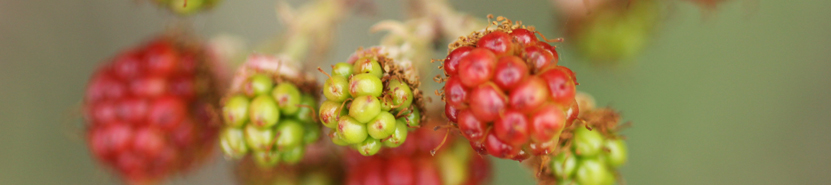
Energy-focused productivity increase aimed project for
the flour factory
Absolutely, almost for all the communities in the world the “flour” is one of the indispensible of fundamental foods. Hence that, every day billions of tons of flour are consumed by the human being routinely. So as to meet that much of demand, flour milling plants have always been searching to increase their daily production capacities more and more. Therefore, in today’s technically-advanced flour milling plants it would not be a surprise to see computer-aided technological machines, working with high speed. Additionally, for capturing high production rate, almost all medium and large-sized flour factories all around the world have highly automated remote controlled production lines. As a dramatic result of those developments, huge amount of electricity have been being consumed for the high capacity flour milling in the factories. Especially for the cleaning and transportation of the raw wheat and bran, there is a strict need of use of highly air-pressured pneumatic and elevation systems which absorbs huge amount of unit of electricity per working hour(s). Besides that, for the raw wheat breaking and wheat plansifting there is also a need for continuously electricity absorption for hours.
However, though that picture of flour milling does not seem so pleasant, it cannot be thought as a desperate, unsolvable issue; to re-engineering the process flow so as to decrease per unit electricity consumption. After a detailed analysis through the production is made, one can easily say that there are extramendous potentials exist along the production line in order to decrease total consumption. Firstly, as a rule-of-thumb some measurement systematic must be created. The relationship between unit production made per time and electricity consumed at same amount of time should be defined in order to analyze and monitor electricity consumption efficiency per production. After so, it would be meaningful to shape optimization solutions providing electricity saving. All of the added-values that would be gained are indeed the successes enrich the decrease in electricity consumption per unit of good producing. So, the indicators of electricity efficiency must be defined with an advanced engineering approach. By the way, increase in productivity rate would be measured easily. The roadmap could be made under the reference of the measurement results of those indicators. To answer the questions “how” and “when” while finding the improvement solutions is the milestone and it can only be done by creating the necessary meaningful measurement indicators in detailed. As a few of examples, the following ones can be given:
Electricity-Focused Productivity and Efficiency Measurement Indicators
- Amount of flour produced (kg)/Amount of electricity consumed (kW) (per hour)
- Amount of electricity consumed/ 1 kg of flour producing
- Amount of electricity consumed per 1 hour of pneumatic working
- Amount of flour cleaned per 1 hour of raw wheat cleaning machine working/ Amount of electricity consumed per 1 hour of raw wheat cleaning machine working
- Amount of flour produced/ 1 hour of electricity consumed in means of kW